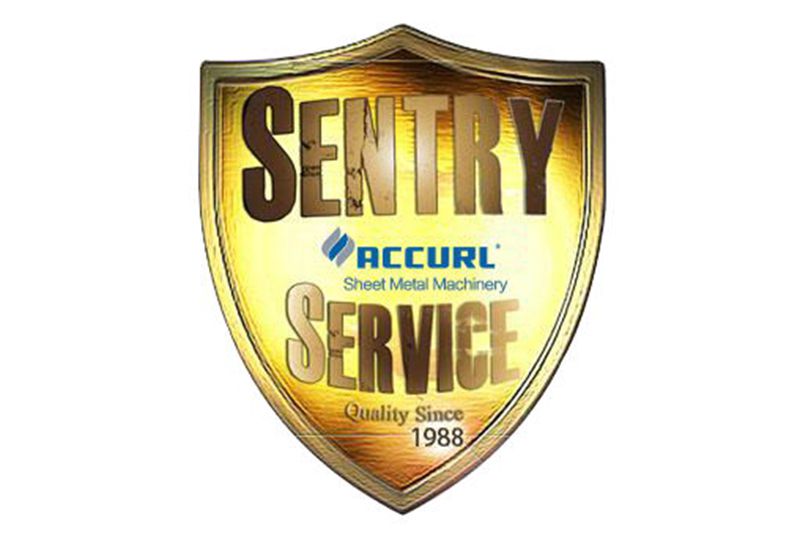
Thanks to our upgrades and maximum capacity, ACCURL services translate into shorter downtime and on-time job completion.
We believe that by monitoring machine conditions, we can save you both time and money. We use the information collected from the machine library to update the maintenance task list, ensuring your machine runs safely and efficiently.
ACCURL machines are designed to offer years of reliable operation; however, to maintain the profitability of the machinery, proper maintenance and service should be taken into account.
Our service agreements enable customers to stay up-to-date, ensuring that their total cost of ownership is economical. This makes investing in our services a cost-effective option.
Service agreements are the optimal strategy for sustaining the operational life of machinery. By adhering to maintenance schedules, we can reduce the likelihood of costly unplanned downtime and guarantee the ongoing performance of the equipment.
- Perform the calibration
- Perform the adjustment
- Perform the alignment
- Check the machine parts
- Recommend maintenance
- Identify parts required
- Observe and verify proper machine operation
- Identify impending failure
- Recommended maintenance.
- Identify parts required
- Observe and verify proper machine operation
- Identify impending failure
- Preventative maintenance program reduces the likelihood of unexpected downtime.
- Avoid unplanned downtime is more cost-efficient
- Machines offer superior quality outputs while keeping maintenance costs competitive.
- Machines can run at full power and maximum efficiency for long periods of time.
- Safe working environment
- Minimize impact on the environment
- Service fee discount
- Free technical support
- Priority service intervention
- Discount on all spare parts
- Updated maintenance action list
- OEM preventive maintenance program
- Free technical support during office hours
- Professional alignment tools and methods
- Original spare parts, 6 months warranty